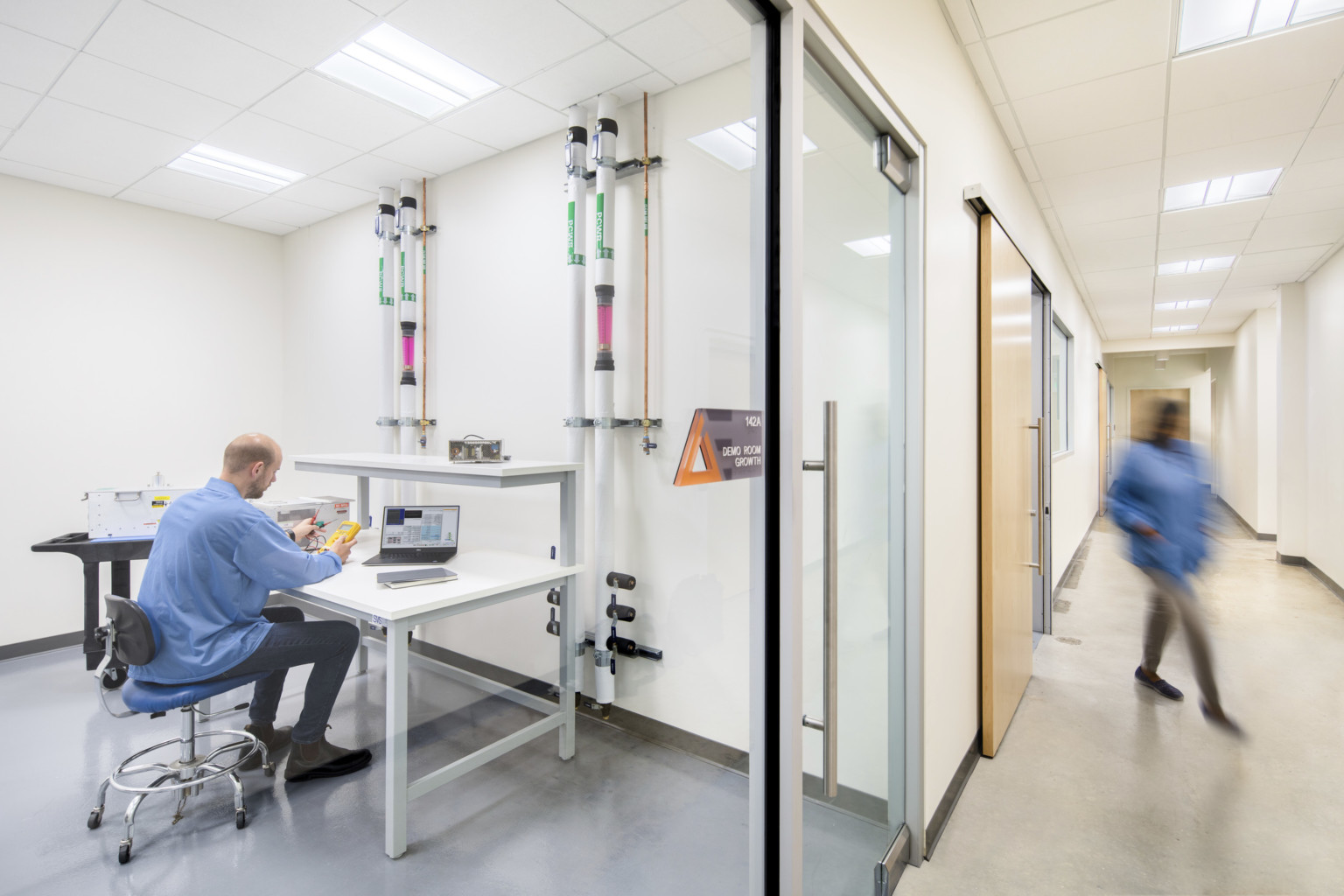
Nine Laboratory Must-Dos
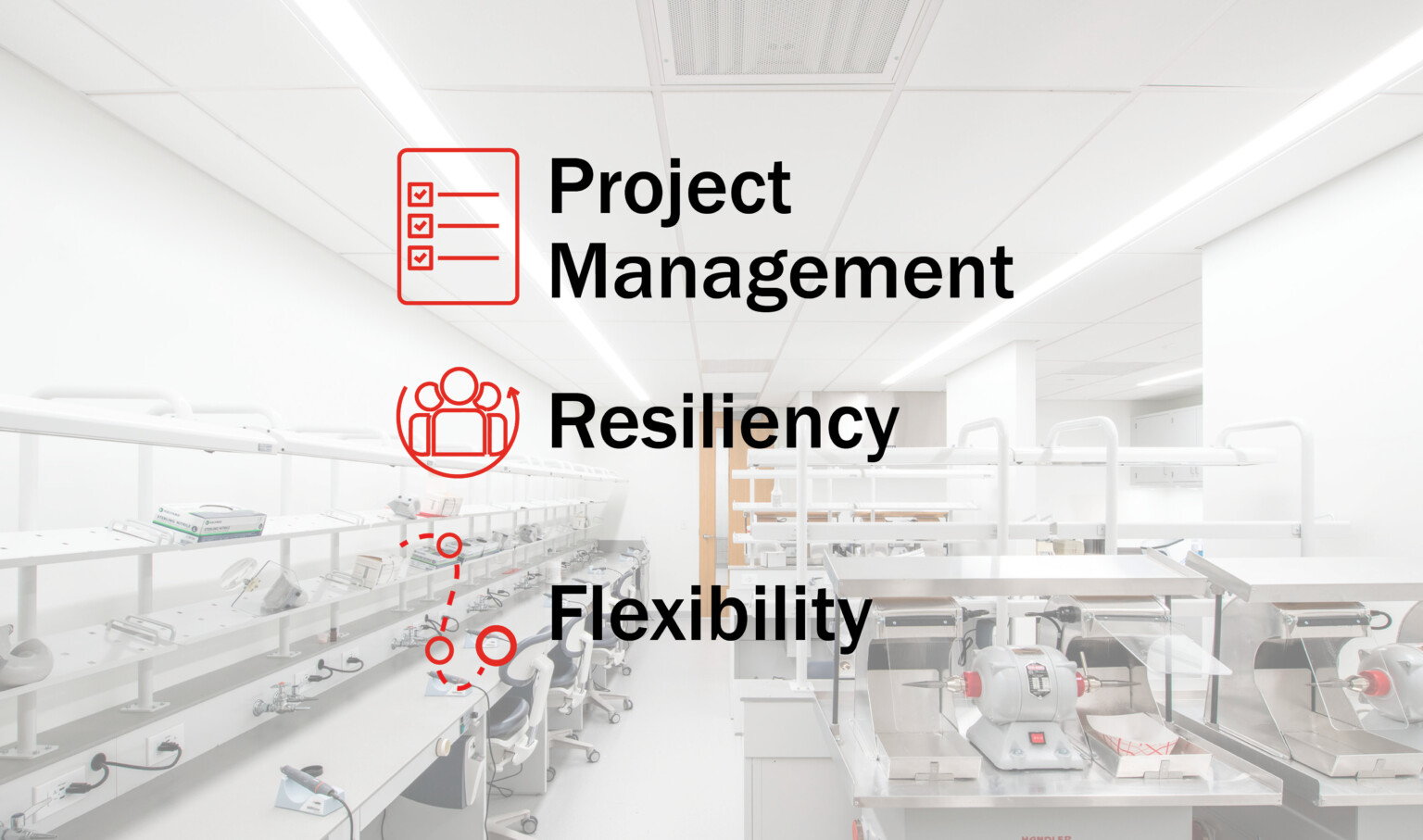
Project Management
Before undertaking the project management of a lab, establish your values and goals. This allows for the identification of any specialty design needs and key players (for example, hazmat). In managing your team, develop clear communication channels between end-users, project managers, and design team; combine with an established project schedule to streamline your operation. And don’t forget to establish design review process, to keep everyone on the same page.
Resiliency
You want your design to last. Going into the design process, make sure you understand your growth schedule, rate, and throughput. This includes: considering the scalability of current processes, accounting for staff increases, and identifying how laboratory support affects both current and future mission statements and business plans. Always plan for ADA compliancy from the start.
Flexibility
Don’t get stuck in a cookie cutter approach to lab design. Consider entire space usage conversion, utility distribution infrastructure, and process flows. Versatility is important for individual workstations, but technicians aren’t the only users to consider; determine the adaptability of research subjects, too.
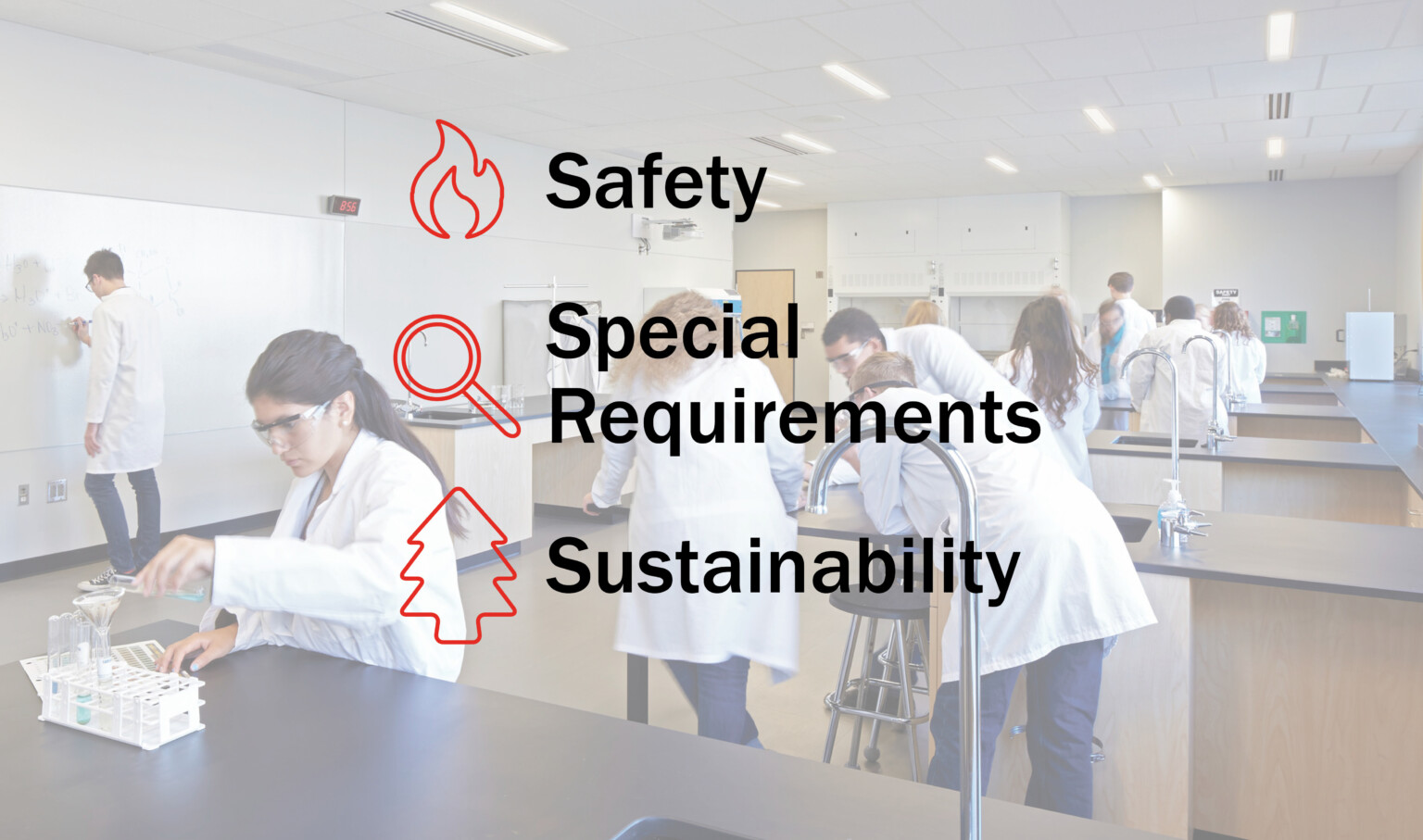
Safety
Identify a building safety officer or Environmental Health & Safety (EH&S) personnel. It’s important to understand the process for storing and handling of flammable liquids and gases, corrosives, and radioisotopes. Determine if there are infectious microbes which will require BSL-3 containment or greater (autoclave). Establish what the protocols are for disposal of waste, either chemical or biological.
Specialty Requirements
Some labs have special considerations. Going in to the process, understand vibration sensitivity or transmittance, as well as any electromagnetic sensitivity or emittance. Identify RFI/EMI/Anechoic Chamber usage, and make known any clean room classifications and isolation requirements. Establish what cGMP requirements and manufacturing practices.
Sustainability
Work with stakeholders to determine building certification platform or values (LEED, WELL, etc.) and consider strategies for energy conservation. Perform building life cycle cost analysis to help inform decisions. Consider internal or local grassroots initiatives.
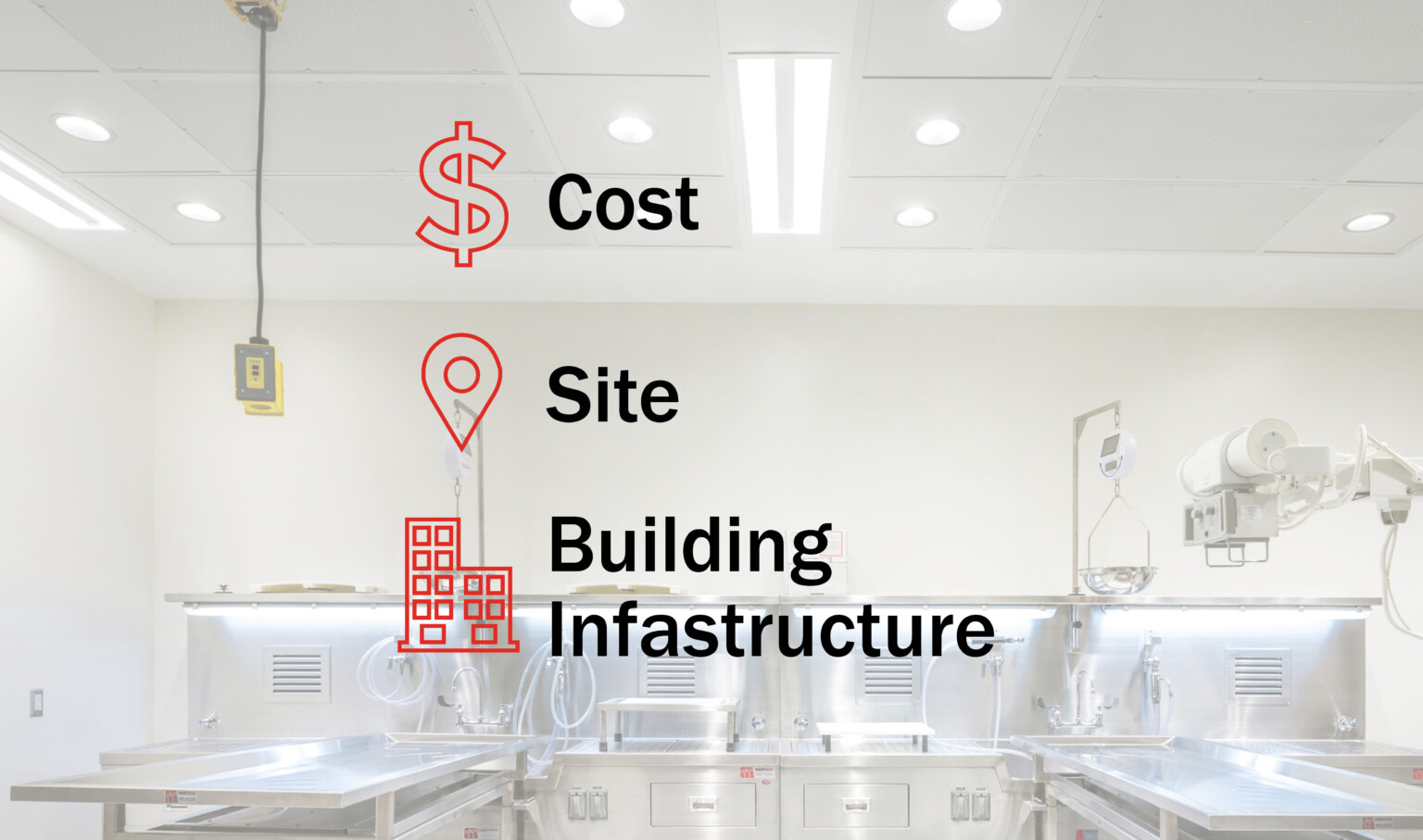
Cost
In determining cost, identify:
- Budget considerations and management;
- Cost implications of project phasing and project delivery methods.
Once these are established, you can also consider:
- Life cycle cost analysis for products, systems, and materials – return on investment
- External or supplemental funding options
- Industry partnerships
- Deferred maintenance opportunities
Site
No lab exists in a bubble. Confirm the site’s zoning requirements, as well as the sensitivity of the surrounding environment. Carefully weigh any harsh environment impacts at the site. Consider the logistics for shipping and receiving samples or goods at the site. Evaluate new build vs. renovation opportunities.
Building Infrastructure
Consider centralized waste collection or treatment and determine a system for centrally treated water – two options are reverse osmosis or deionized. Identify requirements central compressed gas. Understand generator/emergency power and any need for uninterruptable power supply. The extent of building alert systems (BAS) and building management systems (BMS) need to be examined in the design process.